Infrastructure
Showcasing our infrastructure
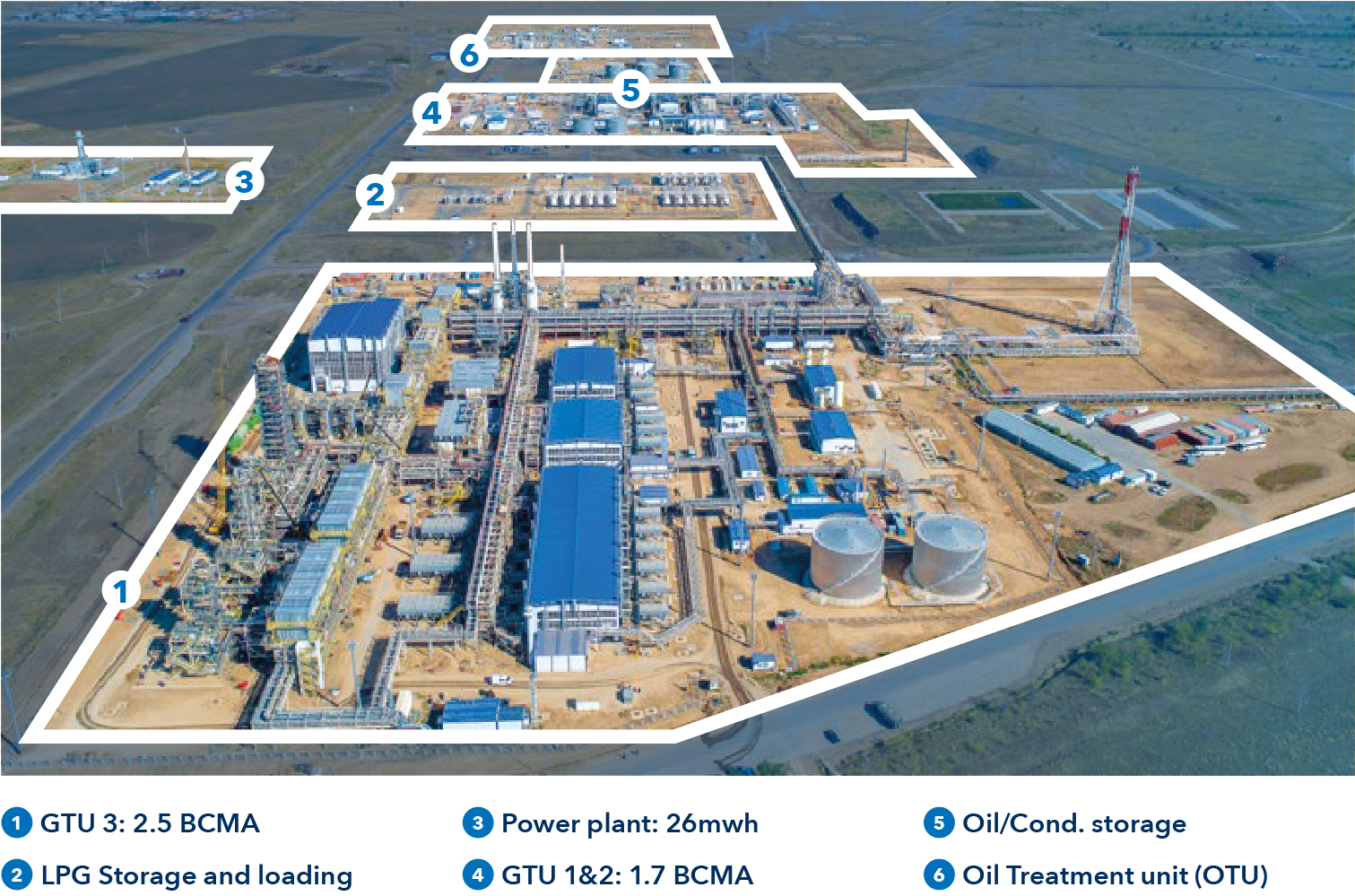
With the re-start of GTU 3, complementing the previous gas processing trains, we have built a world-class infrastructure processing hub that is currently under-utilised but with the potential to support the production and sale of billions of cubic meters of gas in north- western Kazakhstan for years to come.
Oil Treatment Facility
The oil treatment facility (OTF) has a maximum throughput capacity of 400,000 tons per annum. The OTF associated infrastructure includes a gas-lift facility that was commissioned in 2015 and a liquid hydrocarbons pumping station transferring crude oil and stabilised condensate via the liquids pipeline to the rail loading terminal.
In 2024, 0.99mmboe of crude oil and 2.56mmboe of stabilised condensate (including third-party volumes) were transferred through the pipeline from Field to Terminal.
Raw Gas Treatment Facility
The gas treatment facility (GTF) is designed to treat raw gas from gas condensate reservoirs (and the associated gas coming from the OTF) into condensate, LPG and dry gas with a by-product of granulated Sulphur. The gas treatment facility includes three gas treatment units GTU 1,2 & 3 which have the capacity to treat 4.2 billion cubic meters of raw gas per annum.
Low-pressure system
A low-pressure system has been installed to facilitate the reduction of the GTF inlet pressure from 42 to 8 bar, to prolong the run-life of wells, primarily gas-condensate. Installed capacity of gas compression is 48,000 standard cubic meters per hour and all gas-condensate 10 wells are flowing through the low-pressure system as of the end of 2024.
In 2024 a new project (LPS3) to increase low pressure system was initiated with an additional capacity of 10,400 standard cubic meters per hour. Project completion is expected in Q3 2025.
Gas lift system
The gas-lift system is designed to enhance oil and gas-condensate production. The system consists of three gas-lift compressors with a total capacity of 54,000 standard cubic meters per hour.
Currently, the compressors are running at ca. 44,000 standard cubic meters per hour. Total capacity (54k SM3PH will be realised by implementing the Low Pressure capacity upgrade. There were 31 active wells running with gas lift (22 oil wells, 9 gas-condensate wells).
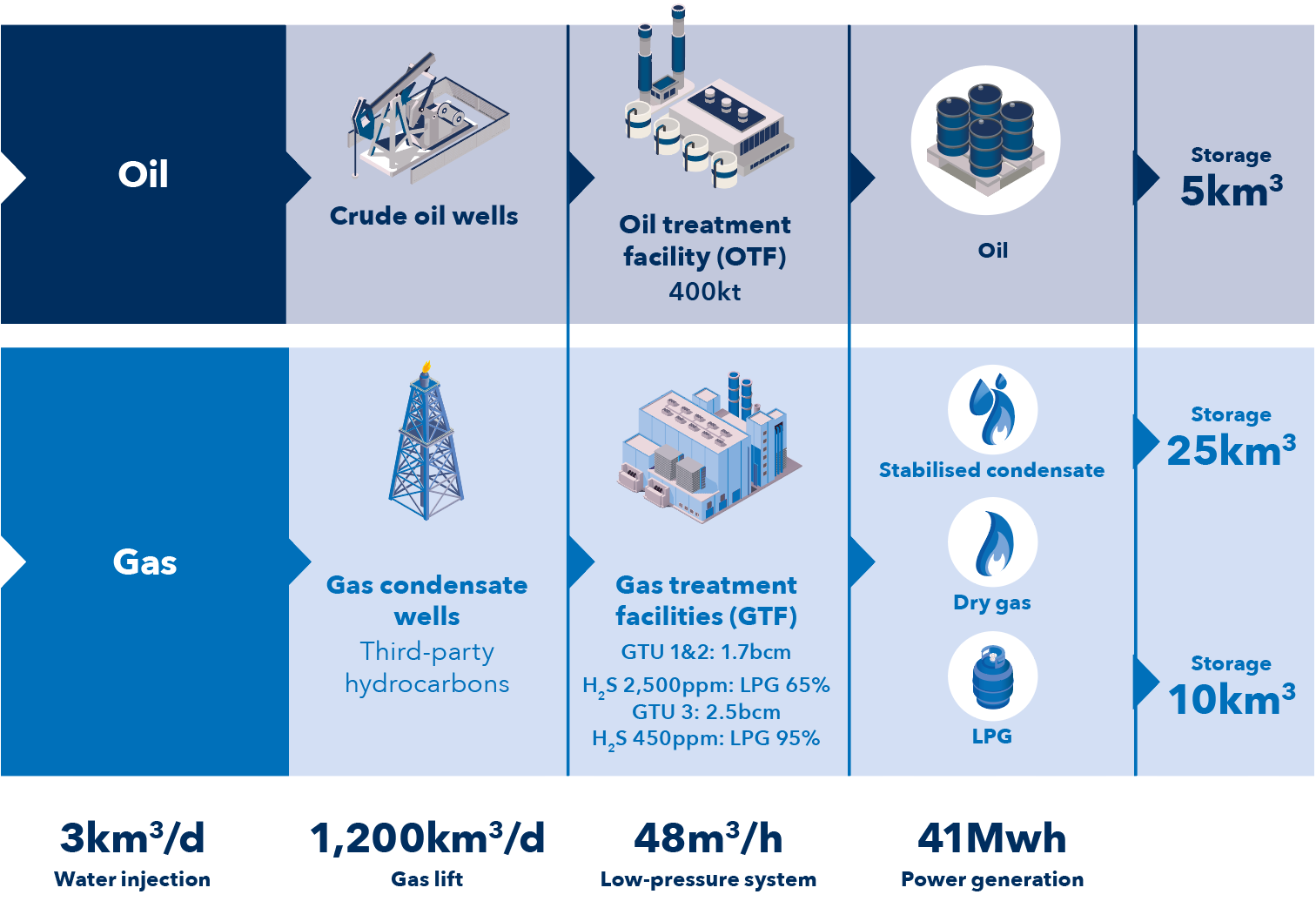
Power generation plant
The gas-fired power generation plant is linked to the GTF and has an electrical power output capacity of 26 MW. The generated capacity of the plant is sufficient to meet the existing and the maximum future need. Backup generation capacity of up to 15 MW is available at the processing facilities.
Storage facilities
Nostrum has over 35,000 cubic meters of storage capacity for liquids at its field site and rail loading terminal.
Gas pipeline
Nostrum has its own 17 km dry gas pipeline which is linked to the Orenburg-Novopskov gas pipeline. The pipeline has sufficient capacity to export the entire GTF maximum production capacity dry gas volumes.
Liquids pipeline
Nostrum has its own 120 km liquids pipeline that runs from the field to the Company’s rail loading terminal in Beles (near Uralsk). The pipeline has a maximum daily throughput capacity of 3,500 t/d.
Rail Loading Terminal
Nostrum has its own automated rail loading terminal at Beles, located near the city of Uralsk, that receives all produced crude oil and condensate and has a daily capacity of 5,000 t/d.
KTO pipeline connection
Nostrum has constructed a secondary crude oil pipeline to enable export sales from its rail loading terminal via the Atyrau-Samara export pipeline operated by KazTransOil (KTO). The connection to the KTO pipeline has enhanced the Company’s ability to maximise crude oil netbacks through the commodity cycle.
Sulphur Recovery Unit and Incinerator
In 2024, modifications on the Sulphur Recovery Unit to handle higher H2S levels, necessary for processing third-party gas like Ural O&G have been completed. This enables H2S processing using either the direct oxidation or Claus process.
In parallel cracks at various heights of the 62-meter incinerator chimney identified in 2023 by drone inspection were repaired.